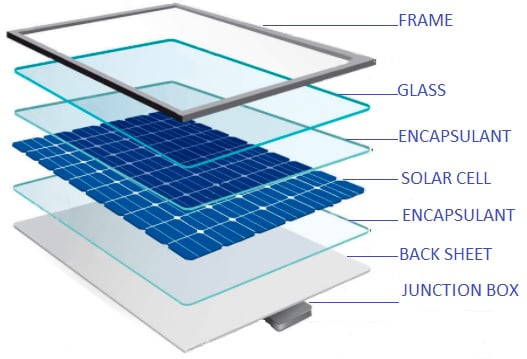
WHY THE SIMILAR SOLAR PANEL SPECIFICATIONS SHOW DIFFERING RESULTS??
QUALITY. The obvious answer comes to the mind. So, during the decision making, understanding Solar Panel QUALITY Problems will help us take better decisions
In solar Plants during the selection, how do we arrive at a decision? Usually, we compare the important specifications such as – panel output power, warranty terms, panel efficiency and maybe one or two specs. And when we compare different brands on these specs, the pattern of thoughts that come to the mind are on these lines:
- All the brands have similar solar panel specifications in power ratings.
- All the brands have similar solar panel specifications in performance guarantee.
- The different brands have more or less similar solar panel specifications but there is a significant price difference between the brands, with no perceptible rationale behind it.
- I am getting the same warranty terms from all, so even if I purchase a lower-priced brand, it will not make much difference in the solar plant.
This logic seems to be correct, but this logic miserably fails us. Why? The reason is our partial knowledge leading to wrong assumptions:
- We believe that the similar solar panel specifications given by all brands are True. They will give similar results. But, this is far from the truth.
- We fail to consider the most important aspect- THE SOLAR PANEL QUALITY PROBLEMS.
To understand, let’s delve a bit deeper into the specifications and the Quality aspect both.
Why its misleading to compare the brands with similar solar panel specifications only?
Let’s consider the two of the most important specs that we compare, Power Rating and the product warranty.
Similar Power Rating: Suppose we consider different solar panels with similar solar panel specification of 330 W panel. It means the panel produces 330 W of power ratings under STC (Standard Testing condition). The STC is taken as radiation of 1 kW/m2, a cell temperature of 25°C, and no wind to compare the panel under similar testing conditions.
In actual conditions
- the irradiance(radiation) differs from season to season and place to place,
- the cell temperature is much higher leading to losses,
- the wind condition has to be considered.
And as such the actual output varies significantly from the STC. The output of different panels are not the same at varying conditions of STC. For this a measure at NOCT (Nominal Operating Cell Temperature) is used, which is also not accurate but gives a better idea of solar power output.
The degradation happens in energy production with passage of time. The rate of degradation is not the same for different brands.
The soiling (dust accumulation on panel), the environment, the shading all affect the solar power output. Hence the output is very different from the nameplate of the solar panel.
In independent surveys, significant variance in power ratings from the nameplate has been found even in STC. In similar external conditions, the power output has been found to be different between different panels of the same rating. Hence the name plate power rating gives a misleading picture.
Reference: Be aware with solar panels quality
Similar Warranty Terms: Suppose we consider different solar panels with similar solar panel specifications having same warranty terms. While the warranty terms may be the same, the warranty experience- ease of getting it, the quality of replacement etc. that we get is not the same. What we fail to understand is that:
- The warranty period is long and the chances of the brand not lasting the warranty period are considerably high. The falling prices, rapid launches of better products, fast-paced technology, obsolescence of products, changing government policies and increasing competition makes survival very tough. If you search on the web, you will find many articles with details of solar companies who went bankrupt or closed the solar panel manufacturing business.
- The ease of claiming and getting warranty differs between brands.
From specifications, as explained above the conclusion can be misleading. The life of the solar Panel and energy production depends on the quality of the panel AND NOT ONLY ON THE SPECS.
Now that you have understood the fallacy of the above thinking process, let’s understand the factors that lead to the solar panel quality problems. Understanding the problems and the faults arising, as a result, will enable us to make a more informed decision.
FACTORS LEADING TO THE SOLAR PANEL QUALITY PROBLEMS:
There are four main factors leading to solar panel quality problems:
01. The components used to make it
02.The Process of Solar Panel Manufacturing
03. The packing and handling of the panel.
04. The designing & installation of the solar plant.
All the four factors are important but here we will cover the first two points as they are directly related to solar panel quality. The other two solar panel quality problems are not directly associated with the quality of the solar panel.
This will help us to decode the faults that come in the solar panels due to the problems in solar panel quality.
So, coming to the first point – understanding the layers of the solar panels, the components used in making them and the solar panel quality problems associated with it.
01. THE SOLAR PANEL QUALITY PROBLEMS DUE TO THE COMPONENTS USED IN PANEL:
The quality of the components used in the solar panel is not the same between all brands, but it makes a huge difference in the price of the solar panel. Let’s look at each layer of the solar panel to understand its effect on the quality of a solar panel.
01.Solar Frame: The solar panel frame forms the top most layer of the solar panel. It has two important functions: a. It binds and provides protection to all the internal components. b. It provides the mounting attachment points.
Frame made of Anodized Aluminium with clear coating increases the corrosion resistance. It should have :
- A high Tensile strength to withstand wind and snow impacts.
- There should not be any cavities so that it collects water.
- It should have a flat tapered edge, where the frame meets the glass, this reduces the shading, allows water to run off and prevents the accumulation of dust and soil.
- The solar panel should not have sharp edges.
- It should be earthed throughout and should be electrically conductive.
- The materials used to join Aluminium and glass together are important to avoid stress build-up because the expansion and contraction ratio of the two are different.
02. The tempered glass: It is a transparent visible layer of the solar panel. It protects solar PV cells against damaging external factors, such as dirt, water & vapour. It, therefore, is also an important barrier material of the solar panel. The glass also offers low reflection, high transmissivity, and high strength.
- Usually, 3 to 4 mm glass is used. Thicker the glass more the stability. Cheaper brands may use 2.5 mm glass.
- The solar panel glass should be rough for proper lamination, it is not standard smooth glass.
- Anti-reflection coating should be done before tempering. The more light the glass absorbs the better will be the panel efficiency.
- The AR (Ant- reflex) coating can cause an increase in solar absorption by 2.5%.
03. Encapsulation foil forms the third and fifth layer of the solar panel, covering the solar cell. It should contain a UV filter. UV wavelengths create heat, which can reduce a cell’s efficiency. For a manufacturer, adding this increases costs and production time. UV filters are the most expensive component of a solar panel, hence it is ignored by cheap brands.
04. The solar cell: This is the core, the costliest and the main constituent of all the layers of the solar panel. It converts solar energy into usable electrical energy. Manufacturing the solar cell requires huge investment. Solar cell manufacturers are few, solar panel manufacturers are many. Most of the small players, non-serious solar players purchase/import solar cells. The solar cell converts solar energy into usable electrical energy; hence the quality of the solar panel is very important.
05.The back foil, forms the last layer of the solar panel. It protects the solar panel from moisture, dust coming from below the panel. The poor quality of the back sheet can deteriorate the life of the panel when exposed to sunlight.
is it from t and
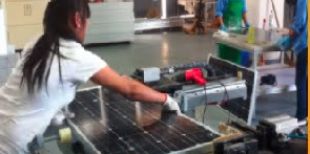
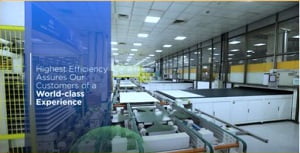
2.THE THE SOLAR PANEL QUALITY PROBLEMS DUE TO THE PROCESS OF SOLAR PANEL MANUFACTURING :
Both the pictures above are of the manufacturing process of the solar panel. Can you observe the difference between the two?
You may have correctly observed… One picture is of the panel being made by a manual process and the other of an automated process in the TATA Manufacturing Plant.
The manual process leads to inconsistent quality and probability of higher human errors. This leads to more solar panel quality problems.
So, what difference does it make?…. Now that we have understood the quality differences in the panels, let’s try to analyse and understand further the faults that come in the solar panel due to the quality issues.
SOLAR PANEL QUALITY PROBLEMS: DECODING THE FAULTS IN SOLAR PANELS
Now that we have understood the difference in the components and the manufacturing process of the solar panel- let’s try to decode the faults in solar panels. Let’s try to understand the solar panel quality problems and why the quality of the panel is so important.
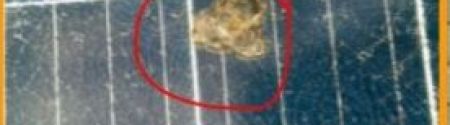
HOT SPOT
Meaning: Solar Panel fault in which Warm spots form on the solar panels due to overheating
Cause: In the Solar panel, the cells are connected in a series in a string. Heating occurs when a large number of series connected cells cause a large reverse bias across a low current producing defective cell, leading to large dissipation of power in the poor cell. Essentially the entire generating capacity of all the good cells is dissipated in the poor cell.
The reasons for the hot spot are: i. Badly soldered connections on the panels. ii. Structural Defect in the solar cells,iii. Cell mismatch, iv. Partial shadow, dirt, sand etc. on the panel.
Effect: Causes short circuit and reduces the performance and lifespan of the solar Panel. They can cause loss of up to 20%-25%.
Reference:Hot spot susceptibility and testing of PV modules
Detection and analysis of hot-spot formation in solar cells
Hot-spot measurements on crystalline silicon solar cells with different reverse current characteristics

MICRO-CRACKS
Meaning: Solar Panel Fault in which Microscopic cracks and tears caused in the solar cells, not visible from the naked eye.
Cause: Can happen during production in a solar module or during shipping or by careless handling during installation.
Effect: It may not necessarily cause immediate production loss, but it can grow into larger cracks over time, with a change in seasons and weather conditions. The panel’s performance decreases in direct proportion to the number of broken cells. As the cells are wired in the series in the solar panel the production of the entire panel gets affected. They can cause a loss of 3% in the short term and 20% in the long run.
Reference:
Review of Microcrack Detection Techniques for Silicon Solar Cells
Analysis of different microcracks shapes and the effect of each shape on performance of PV modules
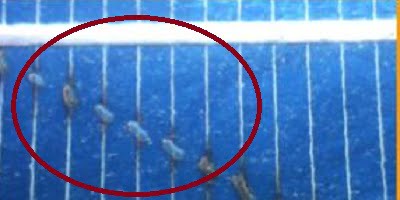
SNAIL TRAIL
Meaning: Solar Panel Fault in which Snail trail is formed. Snail Trail is a discolouration of the panel which usually manifests after a couple of years of production.
Cause: Snail trails are caused in the solar cell due to the use of defective front metallization silver paste in the manufacturing process or due to the microscopic cracks in the solar panel. Due to this the moisture penetrates the back panel and diffuses to the cell surface. This leads to oxidation between the silver paste and the encapsulation material called EVA (ethylene vinyl acetate), releasing silver oxide, acetic acid and hydrogen.
Effect: The effect is visible from the back of the panel to the front of the panel and causes a chemical breakdown on the front of the panel. This results in a reduction in the panel’s performance and is visible as ‘snail trails’. They can cause a loss of 9% to 20% on the Solar Panel.
Reference: Snail Trails and Cell Microcrack Impact on PV Module
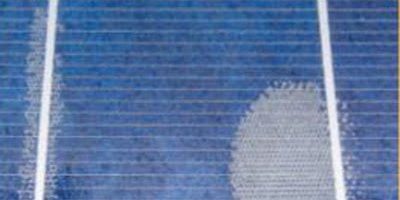
DE LAMINATION
Meaning: Solar Panel Fault which occurs when the bond between the plastics (on the back) and the glass (on the front) separate.
Cause: Panels are made of the glass layer, the solar cells and the back sheet. These layers have to be laminated under vacuum so that they are air- and water-tight. If the vacuum is not properly done then the moisture penetrates into the panel causing Internal corrosion (rusting) and de lamination (detachment of the laminated components). The probable causes of these are: i. Inferior plastic. Ii. The glass or plastic are not clean or iii. The laminating machine is inferior and not regulating pressure or temperature.
Effect: It is visible as darker spots on the panel. This often starts at the edge of the panel and if severe will spread across the rest of the panel. If the metal conducting part of the panel is corroded it leads to a significant reduction in the panel’s production. The panel’s production will decrease in direct correlation to the size of these darker (corroded) areas.
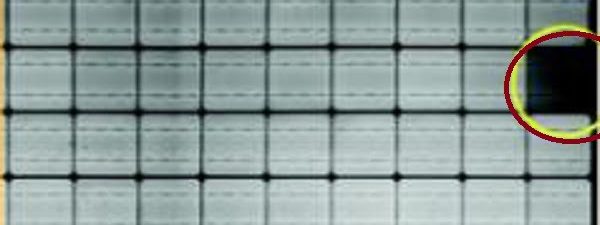
LID EFFECT
Meaning: Solar Panel Faults which happens due to Light Induced Degradation.
Cause: It happens within the first few months of installation by exposure to sunlight. The cells have either P-Type or N-Type electrical properties to conduct electricity. The P-Type cells use Boron as the doping materials. The oxidation of Boron causes LID effect.
Effect: This can lead to losses up to 0.5% to 3% as per manufacturer datasheet. However, as per test results published by on the LID effect and the results were published by Sunvoltaics, it was found that the variance was found to be 0-10%. More than 57% of the cells showed degradation of the module beyond 3% within 3 days of light exposure.
PID EFFECT
Meaning: PID stands for ‘Potential Induced Degradation’. It is also a fault related to the solar Panels.
Cause: This problem arises when the modules are in strings, and are operating at a high voltage (1000 V or less), combined with humid and warm weather. The Dust and deterioration of glass may release Sodium ions causing PID phenomena.
Effect: The PID affected module has “black” cells, closer to the frame of the module. The consequences of this effect are an ongoing reduction in performance and accelerated ageing of the PV panel. They can cause a loss of up to 30% on the solar Panel as per Wikipedia
*For further read on LID & PID you can follow the article written by Niclas in Sinovoltaics.com: devastating effect of LID & PID
Now that you have understood the faults I am sure you must have understood why the point no. 3 (The Packing and handling of the panel)and no.4 (The designing & installation of the solar plant given above are also important.
HOW TO ASSESS THE QUALITY OF THE PRODUCT:
Most of the time you will find the specs to be more or less the same between brands on paper. This makes it difficult to choose the product on the basis of specifications. Moreover, the specs given are not a true basis of evaluation of the brands, as explained above.
Quality is more important than the specs, but it is difficult to assess the quality. So, this leads us to the next question- How to assess the Quality?
It is difficult to check the quality, the product will prove its quality only in due course of time. However, Quality can be inferred indirectly by the under given guidelines :
- Manufacturer is a Tier-I or Tier-II Brand.
- International Certifications, whether they comply with all the International standards.
- Past Performance, how long has the brand been in the solar industry, what is its past performance.
- The awards and recognitions received by the brand from international and established agencies.
- Customer reviews received by the brand for the Past performance.
- Ease of claiming and getting the warranty
- The chances of the company surviving the lifetime of your plant: whether the brand is growing more than the industry average.
- Whether the brand is Quality conscious or Cost conscious
CONCLUSION:
A good reliable solar brand and vendor with credentials can save you from many future troubles.
Moreover, the higher initial costs get compensated by better energy efficiency and output in a few years.
So, one should always go for a reputed, established brand to get best value for money and peace of mind. This is the simplest and most safe decision which protects from many future problems. with
testing
Nice
Thanks
Very informative
Thanks